
Industrial saws and cutting machines
Industrial saws and cutting machines
Industrial saws are essential tools in various manufacturing and industrial settings, from metal fabrication to woodworking. They are used to cut through a wide range of materials, from non ferrous metals like aluminum or copper to plastics and laminate, and are available in different types and sizes to suit different applications. In this article, we will explore the different types of industrial saws and their uses.
Importance of industrial saws
Industrial saws play a crucial role in many industrial applications, where precision cutting is required. These saws are used to cut through a variety of materials, from metal pipes and bars to plastics and wooden planks and panels, with precision and accuracy. Without these saws, it would be challenging to create complex shapes and cuts required in many industrial products, from furniture to machinery components.
Different types of industrial saws
There are several types of industrial saws available, each with its specific features and benefits. Some of the most common types of industrial saws include circular saws, band saws, chop saws, and mitre saws. Each of these saws has unique capabilities, making them suitable for different applications.
This article will provide an overview of the different types of industrial saws, their uses, and their benefits. We will explore the features and advantages of each type of saw and provide insights into how they can be used in different applications. Whether you are a professional in the manufacturing industry or a DIY enthusiast, this article will help you choose the right saw for your project.
Circular Saws
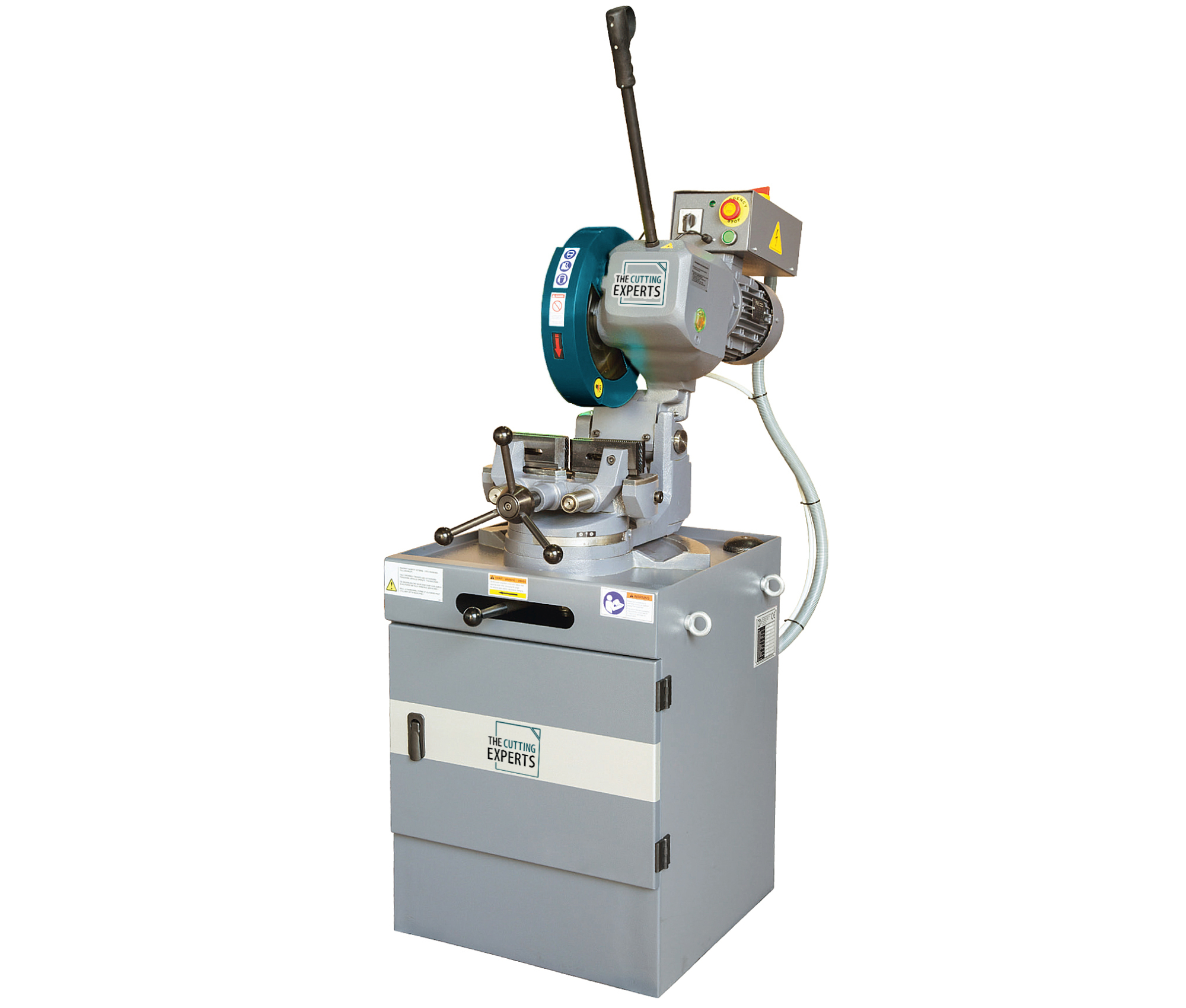
Circular saws are power tools that use a circular saw blade to cut various materials, such as wood, metal, plastic, and concrete. The circular saw blade spins at high speeds, generating the force needed to cut through the material. Circular saws are available in different sizes, ranging from small handheld models to large stationary machines.
Types of circular saws and their uses
-
Handheld circular saws
Handheld circular saws are portable and can be used for a variety of cutting tasks, such as cutting boards, plywood, and metal sheets. They are suitable for use on job sites, where mobility is essential. Handheld circular saws can be corded or cordless.
-
Table saw
Table saw is a stationary table machine that is ideal for cutting large sheets of material, such as plywood and MDF. They have a large, flat table that supports the material being cut and a circular saw blade that protrudes through the table. Table saws are commonly used in woodworking shops. A portable table saw can be a great option for those who need on the job cutting or in smaller spaces, but it may have limitations when it comes to process larger materials, withstand extreme impact or extreme durability.
-
Chop saws
Chop saws, also known as miter saws, are used to make crosscuts and miter cuts in wood, metal, and plastic. They have a pivoting arm that allows the saw blade to tilt and rotate to make angled cuts. Chop saws are commonly used in construction, woodworking and non ferrous metal cutting.
-
Cold saws
Cold saws are used to cut metal, and they have a cooling system that prevents the blade from overheating during use. They are commonly used in metalworking shops and fabrication shops.
Advantages and disadvantages of circular saws
Advantages:
- Versatile, can cut a variety of materials, including nonferrous metals
- Available in different sizes for different applications
- Portable, can be used on job sites
- Efficient and fast cutting speeds
- Suitable for straight cuts and angled cuts
Disadvantages:
- Can produce a lot of noise and dust
- Can be dangerous if not used correctly
- Limited in their cutting depth compared to other saw
Note on metal cutting circular blades
Saw blades come in various types, each with unique features that cater to specific cutting needs. One type of saw blade is the thin kerf blade. These blades have a smaller kerf or width, which means they remove less material and produce less waste during the cutting process. They are also more efficient and require less power to operate. Hi density carbide is often used to make carbide tips for these blades, which helps maintain their sharpness and maximum durability.
Another important feature of saw blades is their tooth design. The triple chip grind (TCG) is a popular tooth design that is commonly used for cutting non-ferrous metals and composite materials such as laminated particleboard and MDF. The TCG tooth pattern alternates between a chamfered tooth and a flat tooth, which reduces chipping on both the top and bottom surfaces of the material being cut.
When choosing a saw blade online or in store, blade size is an important consideration. A laser cut body blade that is too small may not be able to handle the size or thickness of the material being cut, while a laser cut body blade that is too large may cause too much friction and produce excess heat, leading to a poor quality cut. The number of teeth on the blade also affects the quality of the cut. A blade with more teeth produces a nicer, smooth cut, while a blade with fewer teeth can remove material faster but may leave rougher edges.
Other factors that can impact the quality of a cut include the blade's hook angle and the amount of vibration and plate stiffness. The hook angle affects the blade's aggressiveness and its ability to feed material smoothly. Excessive vibration can cause the blade to wander or produce an uneven cut, while a lack of plate stiffness can cause the blade to flex or bend during use. To get the most out of a saw blade, it is important to use the proper blade size and tooth count for the material being cut, as well as to ensure that the blade is properly installed and maintained.
Band Saws
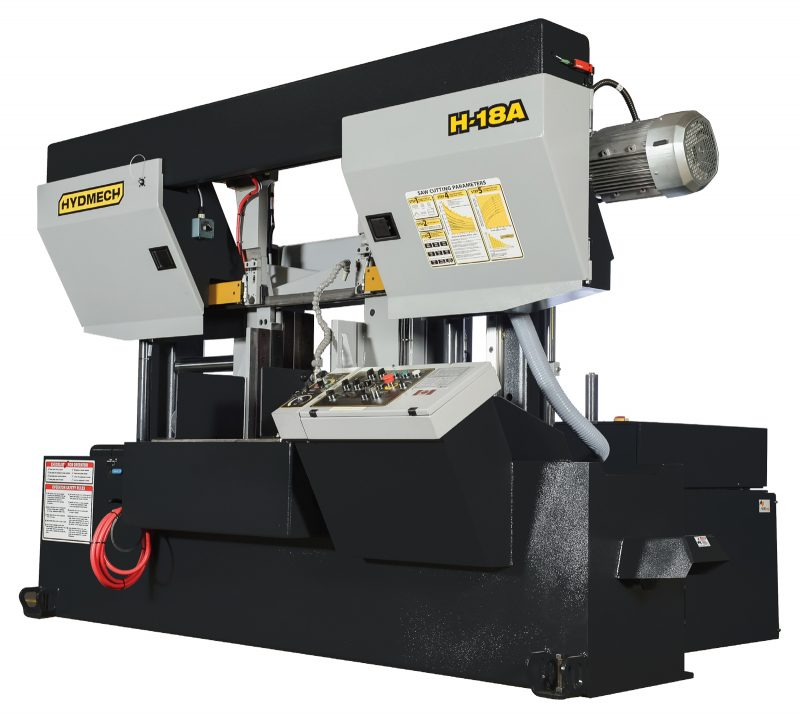
Band saws are a type of industrial saw that uses a continuous, toothed metal band, or blade, to make cuts. The metal blade is stretched between two wheels and rotates in a continuous loop for smooth cuts, allowing for precise and efficient cutting of a variety of materials, including wood, metal, and plastics.
Types of band saws and their uses
There are several types of band saws available in the market today, each designed for specific industrial cutting applications.
-
Horizontal band saws: These band saws are ideal for cutting larger workpieces and are commonly used in metalworking shops. They have a flat cutting surface and can be used to make straight, angled, or curved cuts.
-
Vertical band saws: These saws have a smaller cutting capacity than horizontal band saws and are typically used for smaller workpieces. They are often used in woodworking shops to make intricate cuts.
-
Double column band saws: These saws are designed for heavy-duty cutting applications and have a larger cutting capacity than both horizontal and vertical band saws. They are commonly used in metalworking and fabrication shops.
-
Portable band saws: These saws are handheld and can be easily carried to job sites. They are commonly used in construction and plumbing applications to make quick cuts on metal pipes and other materials.
Advantages and disadvantages of band saws
Advantages:
- Can make precise cuts in a variety of materials
- Can make curved cuts
- High cutting efficiency and accuracy
- Can be used for both production and custom work
- Low blade waste compared to other saws
Disadvantages:
- Limited cutting thickness capacity
- Can be expensive
- Require more maintenance compared to other saws
- Can produce loud noise during operation
Overall, band saws are a versatile and reliable tool for industrial cutting applications. Their ability to make precise cuts in a variety of materials makes them a popular choice for many industries. However, it is important to consider the specific needs of your metal cutting application when choosing a band saw, as they can be expensive and require regular maintenance.
Reciprocating Saws
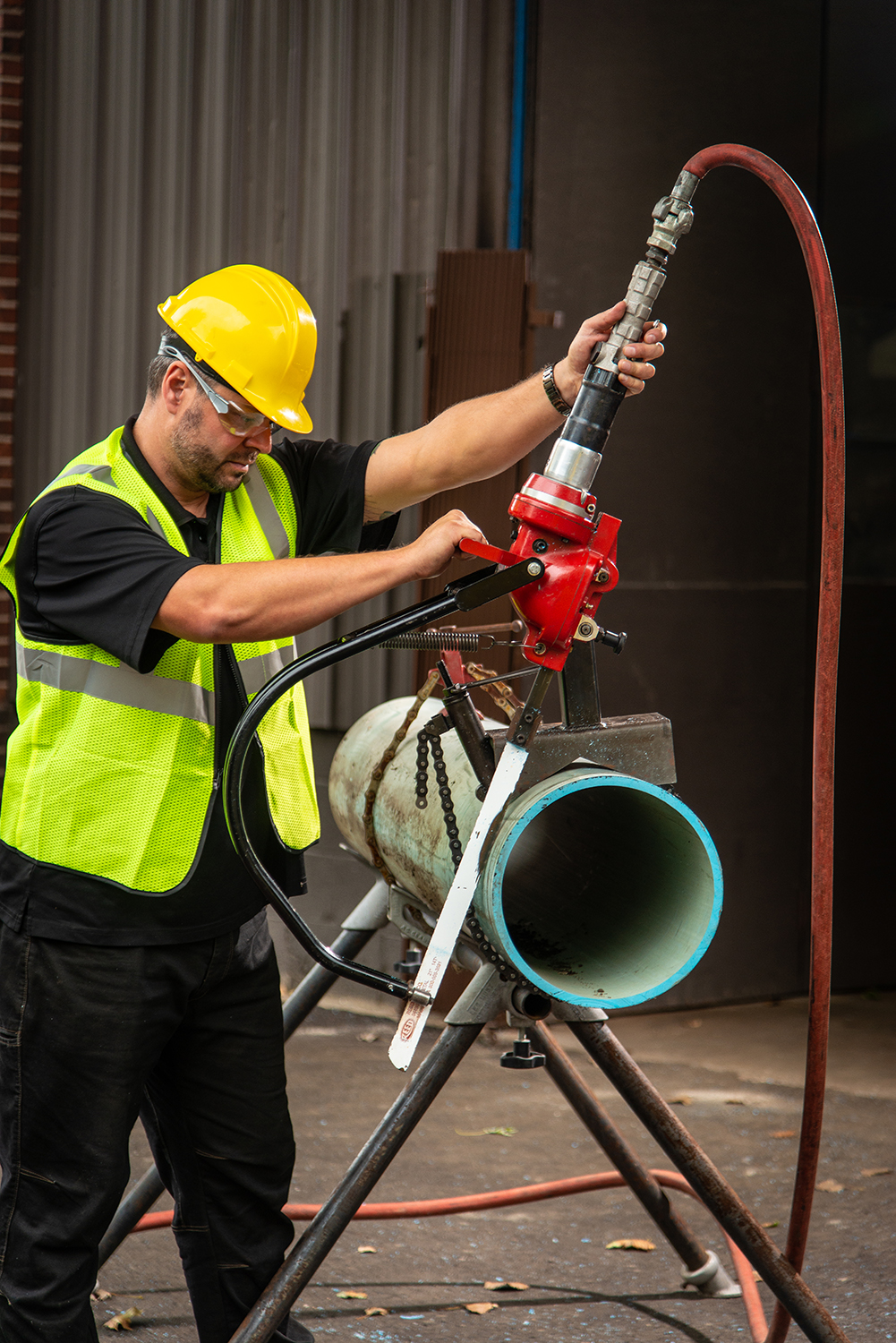
Reciprocating saws, also known as sabre saws or sawzalls saw, are handheld cutting tools with blades that use a push-and-pull motion to create a back-and-forth sawing action. The blade of a reciprocating saw moves in a rapid back-and-forth motion, allowing it to easily cut through a variety of materials, including wood, metal, and plastics.
Types of Reciprocating Saws and Their Uses
There are different types of reciprocating saws, each with their own unique features and uses. Corded reciprocating saws are the most powerful and are suitable for heavy-duty cutting tasks, while cordless reciprocating saws offer greater mobility and are ideal for cutting in tight spaces or hard-to-reach areas. Some reciprocating saws also come with variable speed blade controls, which allow users to adjust the cutting speed to match the material being cut.
Reciprocating saws are commonly used in construction, demolition, and woodworking projects. They are particularly useful for cutting through walls, floors, and pipes. They are also used in metal fabrication, automotive repair, and plumbing applications.
Advantages and Disadvantages of Reciprocating Saws
One of the main advantages of reciprocating saws is their versatility. They can cut through a wide variety of materials, making them a valuable tool for many different applications. They are also relatively easy to use, and their compact size makes them ideal for working in tight spaces.
However, there are also some disadvantages to using a reciprocating saw. They tend to produce a lot of noise, heat and vibration, which can be tiring and uncomfortable to use for extended periods. Additionally, because they rely on a back-and-forth motion to cut, they can be difficult to control and may produce rough or uneven cuts. Finally, they may also produce a lot of dust and debris, which can be hazardous if proper safety precautions are not taken.
Miter Saw
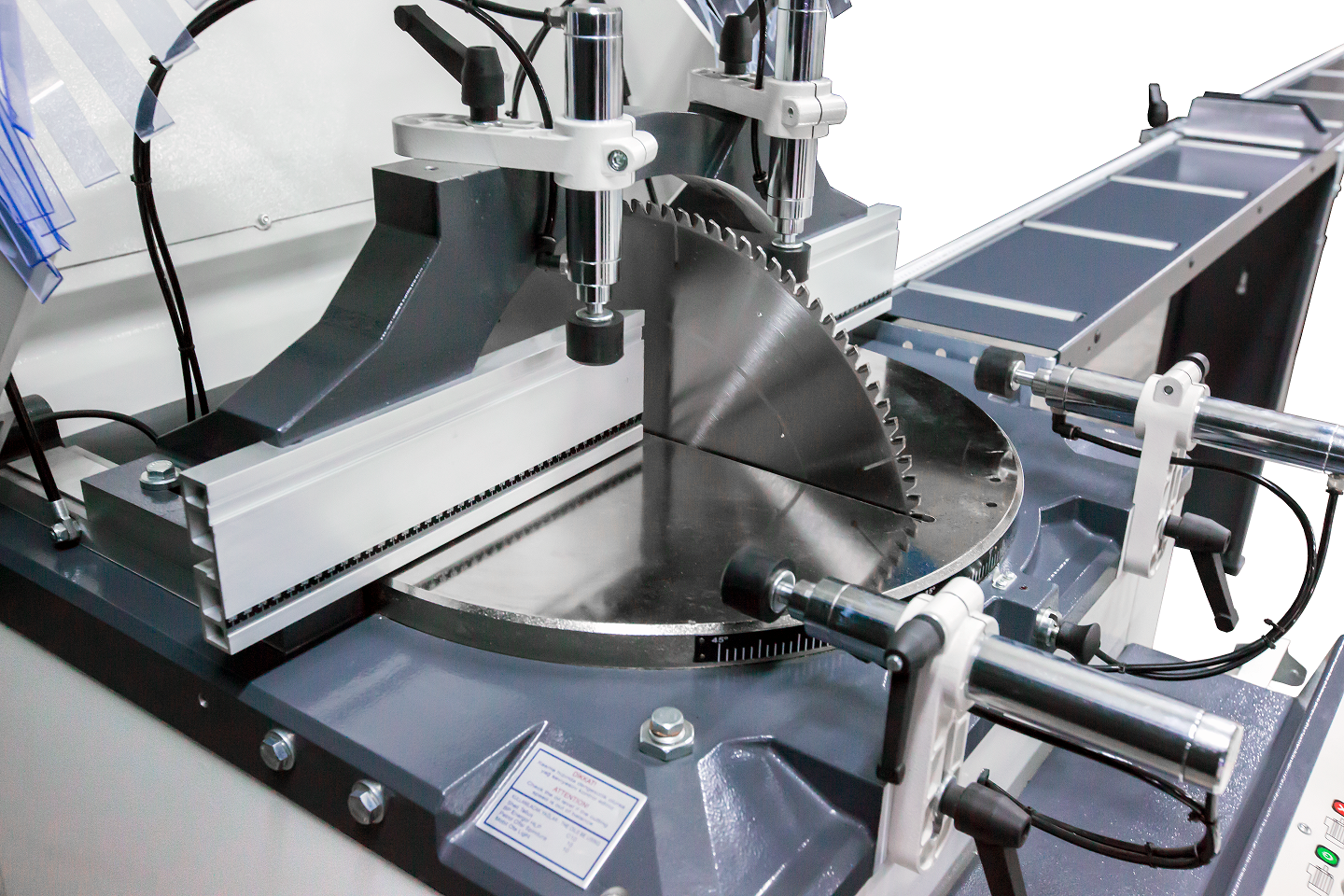
A miter saw is a specialized power saw that is designed to make precise angle cuts in wood, metal, or other materials. They are commonly used in carpentry, construction, and metalworking applications to create clean, accurate cuts at a specific angle. A triple chip grind saw blade can be used on various types of saws, including a miter saw. A TCG (triple chip grind) saw blade is a type of circular saw blade with a specific tooth geometry. It is designed to cut aluminum extrusions, composite materials such as laminate flooring, MDF, and other non ferrous metals. The carbide tips blade features teeth with alternating beveled and flat edges, which help prevent chipping on the top surface of the material being cut, providing a burr free finish. This tooth geometry also allows this great blade to be used with a scoring saw unit to pre-cut the bottom of melamine or laminate panels for a cleaner cut.
Types of miter saws and their uses
There are several types of miter saws available, each with unique features and applications.
-
Standard miter saw: These saws are the most common type of miter saw and are ideal for cutting at a variety of angles, ranging from 0 to 45 degrees. They are used in a wide range of applications, including framing, moulding, and trim work.
-
Compound miter saw: These saws can make both angled and beveled cuts, making them ideal for more complex projects that require intricate cuts. A compound miter saw can tilt in one or two directions, allowing for more precise and complex cuts.
-
Sliding compound miter saw: These saws have a sliding feature that allows the saw blade to move back and forth, enabling it to cut wider materials. A sliding compound miter saw is ideal for larger projects that require cutting wider materials, such as crown molding, melamine, laminate pannels and large trim pieces.
Advantages and disadvantages of a miter saw
A miter saw offers several advantages that makes it an essential tool for many professionals. They provide a nice smooth cut, long life, are easy to use, and can quickly and accurately cut a wide range of materials. However, they also have some disadvantages. A miter saw can be expensive, and some models can be heavy and bulky, making them difficult to transport to job sites for on the job cutting.
Plasma Cutters
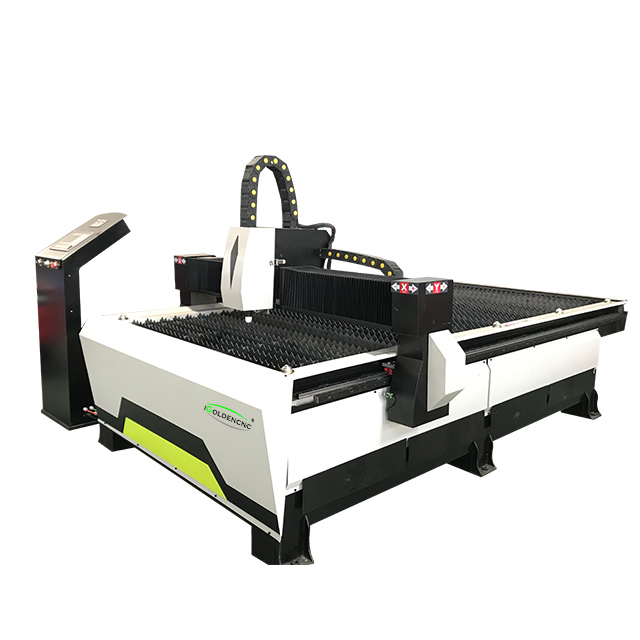
Plasma cutters are tools used to cut metal materials such as steel, aluminum, copper, and brass. They use a plasma torch to heat and ionize gas, which then melts the metal plate, allowing it to be cut smoothly and quickly.
Types of plasma cutters and their uses:
-
Handheld plasma cutters: These are portable and easy to use, making them ideal for smaller metal-cutting jobs in workshops or on job sites.
-
CNC plasma cutters: These are computer-controlled machines that are used in large-scale metal fabrication and manufacturing processes. They allow for precision cuts, making them useful for intricate designs and shapes.
-
High-definition plasma cutters: These use advanced technology to create extremely precise cuts, making them useful for cutting materials with complex shapes or thicknesses.
Advantages and disadvantages of plasma cutters:
Advantages:
- Plasma cutters are highly efficient, allowing for quick and precise cuts.
- They are able to cut through thick metals that may be difficult to cut with other types of saws.
- Plasma cutters create clean cuts, minimizing the need for additional finishing work.
Disadvantages:
- The price of plasma cutters can be high, particularly for high-end models.
- The process of cutting with plasma can produce hazardous fumes and smoke, requiring proper ventilation and safety precautions.
- Plasma cutters may not be suitable for cutting certain materials, such as materials with high thermal conductivity or materials that are highly reflective.
Waterjet Cutters

Waterjet cutters use a high-pressure stream of water mixed with abrasive particles to cut through a variety of materials, including metal, stone, glass, and composite materials. The waterjet stream can be as narrow as 0.1mm, making it ideal for precise cuts and intricate designs.
Types of waterjet cutters and their uses
-
Pure Waterjet Cutters: These cutters use only water and are typically used for softer materials such as rubber, foam, and paper.
-
Abrasive Waterjet Cutters: These cutters mix abrasive particles with water to cut through harder materials such as metal, glass, and ceramics.
Advantages and disadvantages of waterjet cutters
-
Advantages:
- Precise cuts: Waterjet cutters can achieve very precise cuts, even on complex shapes and designs.
- Versatility: Waterjet cutters can cut through a wide range of materials, including metals like aluminum, brass, stone, and composites.
- Minimal heat affected zone: Waterjet cutting produces little heat, reducing the risk of friction, heat buildup, warping or distortion in the material being cut.
- No hazardous fumes: Waterjet cutting does not produce fumes or gases, making it a safer and cleaner cutting method.
-
Disadvantages:
- The price of waterjet cutters can be higher than other cutting methods.
- Slow cutting speed: Waterjet cutting can be slower than other methods, which may not be suitable for high-volume production.
- Abrasive residue: Abrasive waterjet cutting produces abrasive particles that can accumulate and require cleaning.
- Noise: Waterjet cutting can produce a high level of noise, requiring hearing protection for operators.
In conclusion, we have covered a variety of different types of industrial saws in this blog post, with cutting saw blade, including circular saws, band saws, reciprocating saws, miter saws, plasma cutters, and waterjet cutters. Each of these tools has unique features and uses that can make them well-suited for certain metal cutting tasks.
When choosing to purchase an industrial saw, it's important to consider factors such as the type of material you will be cutting, the precision required, and the volume of cutting you will be doing. By carefully selecting the right saw for your needs, you can improve the efficiency and accuracy of your cutting operations and your customers, ultimately improve your bottom line.
We hope that this article has been informative and helpful for our customers and those looking to purchase or learn more about industrial saws. We encourage readers to contact us by email to share their experiences with these tools and ask any questions they may have.
Thank you for reading, and we wish you the best of luck in all of your industrial cutting endeavors!